Conveyor belt systems have revolutionized various businesses by automating tasks and operations that previously required human personnel.
Although initially synonymous with the construction and automotive industries, conveyor belts have become commonplace in many other workplaces too. Warehouses deploy these machinery to deliver goods from storage units to truck loading points. Similarly, resource mining and processing plants rely on belt systems to transfer sensitive chemicals.
According to Future Market Insights, the global conveyor belt market might grow from USD 4.0 billion in 2023 to USD 6.0 billion in 2033. These statistics indicate a significant rise in the adoption of conveyor belt systems.
However, despite their immense benefits, conveyor systems present grievous safety risks to operators. That underscores the imperative of enhancing safety measures at workplaces that rely on this machinery.
Below are noteworthy conveyor belt security protocols to implement in 2024.
1. Safety Measures for All Employees
If you work in an industry that relies heavily on conveyor systems, the first thing to do is educate all your employees on basic conveyor belt use and safety.
Actual conveyor belt operators would require more extensive training.
Note that conveyor belt safety training should be a routine program rather than a one-off exercise.
Be sure to schedule training programs whenever you bring in a new conveyor belt system, especially if the new machinery has advanced features.
2. Safety Measures Before Turning on a Conveyor System
Nearly all conveyor systems are powered. So, it’s prudent to understand where the controls are. That knowledge will come in handy when you need to make split-second decisions during times of emergency.
Inspect your conveyor belt controls carefully before turning the machinery on. These include the knobs, sensors, and programmable logic controllers (PLCs).
Sensors are particularly important as they can detect abnormalities in a conveyor system and trigger an alarm system before anyone gets hurt. Commonly flagged issues include jammed materials, excessive loads, material flow-back, and electrical malfunctions.
Ensure that no employee has modified, disconnected, or damaged the controls. The controls should also be accessible and easy to use.
Besides, check that your conveyor belt has a start-up warning signal. The signal provides ample time for nearby employees safety to clear the area before the machine starts.
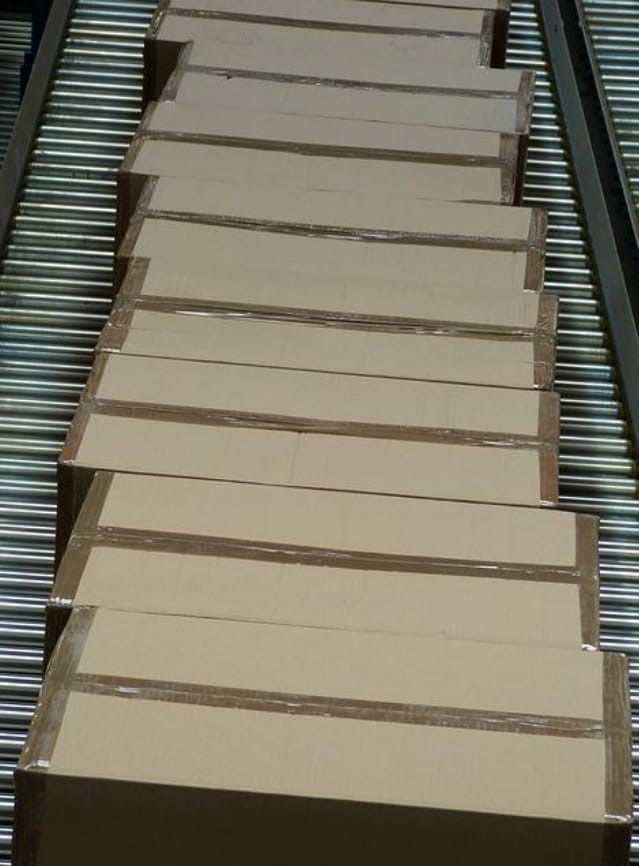
3. Safety Measures Before Using a Conveyor System
Modern conveyor belt systems have guarding that restricts access to moving parts, including belts, gears, and chains. It’s important to ensure your conveyor guarding is securely mounted before running the machine.
That helps to protect operators from accidents caused by moving parts. It also ensures regulatory compliance.
The Occupational Safety and Health Administration (OSHA)‘s general industry standard 29 CFR 1910.219 spells out the guarding requirements for heavy industrial machinery, including conveyor belts. Complying with this regulation can help avoid unnecessary penalties ranging from mere warnings to imprisonment.
One best practice when mounting conveyor guarding is to ensure the guard openings are small enough to keep employees off the machine’s potentially hazardous components.
4. Safety Measures While Operating Conveyor Systems
When exhausted, conveyor belt operators may be tempted to sit or rest their backs on this machinery. The consequences could be devastating, especially if that happens when the machine is in motion.
Note that a conveyor belt is designed to deliver goods, not people, from one point to another. Resist the urge to sit, stand, or even walk along a moving belt.
Moreover, conveyor belt constructions feature pinch points or rotating parts that can catch and rip your clothing into shreds. Worse yet, the pinch points might get stuck and severely damage your limbs.
Below are additional safety measures when working around conveyor belt systems;
- Tuck in loose clothing and jewelry
- Tie back long hair
- Wear personal protective equipment (PPE), including safety shoes, a pair of gloves, a helmet, and hearing protection.
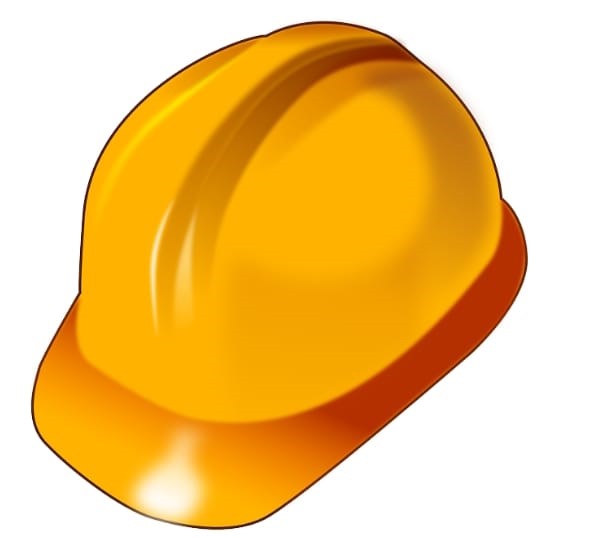
5. Safety Measures When Things Go Wrong
Taking proactive safety measures can help reduce conveyor belt systems significantly.
However, things might still go awfully wrong. And when they do, it’s imperative to act swiftly to mitigate any adverse impacts.
The most critical safety measure here is to press the emergency buttons or pull cords. Such controls help shut down the conveyor system, minimizing accident risks during equipment malfunctions.
After shutting down the machinery, alert your supervisor immediately. Management will determine whether the glitch can be fixed internally or requires a conveyor belt technician’s involvement.
6. Scheduled Maintenance
Conducting routine conveyor belt maintenance can minimize faults in the system by addressing early warning signs of mechanical breakdowns. Regular check-ups are particularly important in uncovering potential issues with the conveyor’s moving parts.
Now, there’s no fixed interval after which you should inspect your conveyor belt systems. The frequency depends on the scope of the examination.
Personally inspect a conveyor belt system for stuck debris before starting off the machine. You could turn the machine on to listen for unusual noises, which indicate damaged or loose components.
However, engage a conveyor belt technician for rigorous check-ups, preferably weekly or monthly. These inspections would focus on deeper issues with the conveyor’s mechanism, such as belt mistracking, bruised joints, and damaged rollers. The technician may also inspect the belt’s electrical system, including the motor and controls.
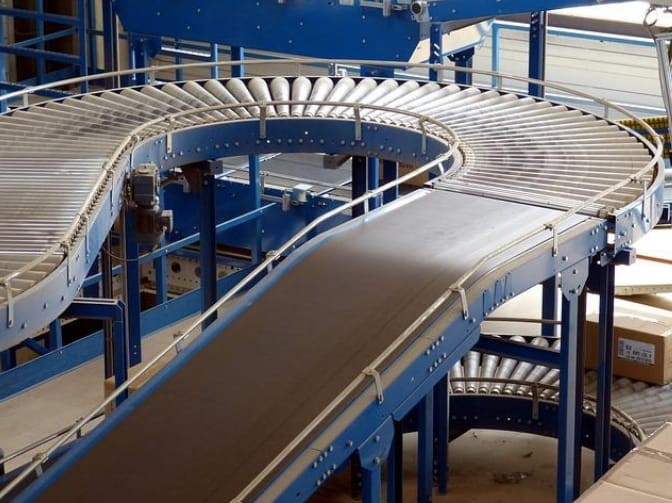
Summary
Implementing a robust safety protocol is paramount in conveyor belt systems industries. It’s the surest way to minimize conveyor-related injuries and the costly litigations that typically accompany such accidents. Besides, proper conveyor safety measures guard against lost productivity resulting from machinery breakdowns.